Özet:
Bu çalışmada, ultra yüksek saflıkta 6N, 7N tohum kristallerinin üretimi için indüksiyon altında radyal kristalizasyon temizliği için bir yöntem sunulmuştur. Soğutma sıcaklığının tohum kristalinin morfolojisi üzerindeki etkisi ile soğutma suyu sıcaklığı, akış hızı ve tohum kristalinin ilave miktarının kristalizasyon prosesi üzerindeki etkisi incelendi ve en iyi temizleme prosesi parametreleri şu şekilde elde edildi: tohum kristal hazırlama sıcaklığı: 278 K; Soğutma suyunun sıcaklığı ve debisi 293 K ve 40 L · h-1; ve tohum sayısı altı ekledi.
Sıcaklığın ve soğutma suyunun akışının kristalleşme hızına etkisi incelenmiştir. Kristalleşme hızı, artan soğutma suyu sıcaklığıyla doğrusal olarak azaldı, ancak artan soğutma suyu akışı ile üssel olarak arttı. Kristalleşme hızı için ilgili denklem deneysel olarak belirlendi ve üç arıtma şeması önerildi. 4 N ham galyum Şema I'e göre saflaştırıldığında, 6 N yüksek saflıkta galyum ve 7 N yüksek saflıkta galyum Şema II ve III'e göre elde edildi. Üç Şema I, II ve III tarafından üretilen yüksek saflıkta galyum saflığı sırasıyla% 99,999987,% 99,9999958 ve% 99,9999958 idi.
1. tanıtım
1970'lerde galyum ve Grup IIIA elementlerini içeren bileşiklerin mükemmel yarı iletken özelliklere sahip olduğu keşfedildi. O zamandan beri galyum (Ga), yarı iletken endüstrisinde bir hammadde olarak kademeli olarak kullanılmaktadır. Son yıllarda, bilim ve teknolojinin sürekli ilerlemesi ve insanların düşük karbon ekonomisi ve yeşil enerji arayışı ile Ga'nın uygulaması tamamen geliştirildi ve modern yarı iletkenler alanında en önemli hammaddelerden biri haline geldi (yaklaşık% 80 toplam galyum tüketiminin% 10'u), güneş enerjisi (toplam galyum tüketiminin yaklaşık% 5'u), manyetik malzemeler (toplam galyum tüketiminin ~% 99,99'i) ve katalizörler ve savunma, fiber optik iletişim, havacılık ve diğer alanlarda yaygın olarak kullanılmaktadır. Şu anda, düşük kaliteli galyum (saflık ≤% 2018) için üretim teknolojisi her geçen gün mükemmelleştirilmiştir. 2017 ABD Jeolojik Araştırması (USGS) istatistikleri, dünya çapında düşük dereceli birincil galyum üretim miktarının 315'de ~ 15 ton olduğunu ve 2016'daki 274 tonluk miktardan% XNUMX arttığını gösteriyor. Yüksek saflıkta galyuma olan talep, yüksek performanslı yarı iletken cihazların geliştirilmesiyle artmıştır, çünkü akımda Cu, Pb, Fe, Mg, Zn ve Cr gibi çok küçük miktarlarda safsızlıklar bile mevcuttur, ticari sınıf galyum büyük ölçekte elektriksel özellikleri bozabilir veya bozabilir. kısıtlamak. Tek kristaller için elektrolitik temizleme, bölgesel eritme, vakumlu damıtma ve çekme yöntemi gibi geleneksel temizleme yöntemleri kullanılmıştır.
Yüksek saflıkta galyum üretimi için, elektrolitik rafinaj işlemi şu anda endüstride yüksek saflıkta galyum üretmek için en yaygın kullanılan teknolojidir. Bununla birlikte, bu geleneksel yöntemlerin yüksek enerji tüketimi, çevre dostu olmama, düşük üretim verimliliği ve rahatsız edici otomasyon kontrolü gibi birçok sorunu vardı. Bu nedenle, günümüzde yarı iletken ve güneş enerjisi endüstrilerinin gelişimi için ileri temizlik teknolojisinin geliştirilmesi çok önemlidir. Galyumun saflaştırılması ve rafine edilmesi sistematik olarak bizim tarafımızdan incelenmiştir. Geleneksel kristalizasyon yöntemine dayanarak, tohum kristalleri ile kristalleşmeyle indüklenen kristalleşme kristallerinin üretilmesi için bir yöntem önerilmiştir. Proses düşük enerji tüketimi, basit ekipman, rahat kullanım ve kısa üretim döngüsü avantajlarına sahiptir. Bu çalışmada, kristalizasyon deneyi, soğutma sıcaklığının kristal morfolojisi üzerindeki etkisini ve soğutma suyu sıcaklığının, akış hızını ve kristalizasyon işlemine eklenen tohum kristalinin miktarını araştırmak için kullanılmıştır. Temizleme işleminin parametreleri, en iyi temizleme işlemini optimize etmek, kristalleşme hızı kontrol denklemini belirlemek ve işlem koşulları altında yüksek saflıkta (6N ve 7N) metal galyum üretmek için incelenmiştir.
2. Malzemeler ve yöntemler
2.1 Proses Tasarımı Image 1, tohum indüksiyonuyla 6N, 7N yüksek saflıkta galyum bisiklik kristal temizleme işleminin üretim işlemini gösterir. Ana adımlar ve prosedürler aşağıdaki gibidir: (1) Kristalleştiricinin saflaştırılması ve temizleyicinin montajı İlk olarak, kristalleştirici, yüzeydeki tozu gidermek için yüksek saflıkta suyla (dirençlilik ≥ 16 MΩ · cm) durulandı. Daha sonra yüzeydeki kalıntı kalıntıları gidermek için 2 saat boyunca ultra saf su içeren ultrasonik bir temizleyici ile temizlendi. Temizleme cihazı, 1b'de gösterildiği gibi monte edildi. (2) 4 N işlenmemiş galyumun ön işlenmesi. 4 N ham galyum, paketleme şişesiyle birlikte bir ocak gözüne yerleştirildi ve ısıtma sıcaklığı, 335 K'ye ayarlandı. Galyum eridikten sonra, erimiş ham galyum bir politetrafloroetilen beher kabına aktarıldı ve 200 saatinde 3 K'de 335 ml 2 mol / 1 HCl ile karıştırıldı. Hidroklorik asit, plastik bir pipet ile aspire edildi ve daha sonra 200 ml 3 mol / l HNO & sub3; behere eklendi, ardından 2 saat karıştırıldı. Ham galyum asit ile yıkandı, ardından üç kez ultra saf su ile yıkandı. Asit muamelesinde kullanılan hidroklorik asit ve nitrik asidin tümü yüksek saflıktaydı ve asit solüsyonunu hazırlamak için ultra saf su kullanıldı. Ön işlemden geçirilmiş erimiş ham galyum (4N) temiz bir kristalleştiriciye aktarıldı. Dolaşan soğutma suyu, kristalleştiricinin su ceketine verildi. Soğutma suyu, düşük sabit sıcaklıkta bir su tankı ve dahili bir sirkülasyon pompası kullanılarak sağlandı. Sıcaklık aralığı 263 ile 373 K arasındaydı, sıcaklık kontrolünün doğruluğu ± 0,1 K idi ve soğutma suyunun akış hızı bir cam rotor akış ölçer ile kontrol edildi. Sıvı galyumun sıcaklığı kritik kristalleşme noktasına düştüğünde, kristal tohumlar ilave edildi ve soğutma suyu sirküle edildi. Bu kristaller, saflaştırma testine başlamak için bir hammadde olarak 7N galyum kullanılarak hazırlandı. Kullanılan prosedür aşağıdaki gibidir: Erimiş 7N galyum içeren bir politetrafloroetilen kap, suyu soğutmak ve kristalleştirmek için düşük sabit bir sıcaklığa getirildi. Kristal çekirdeği dağıtmak ve çekirdeklenme oranını arttırmak için sıvı galyum sürekli bir Teflon çubukla karıştırıldı. Karıştırma işlemi sırasında, sıvı galyumun kristalleşmesi gözlenmiştir.
Üç yollu bir anahtar değiştirildi ve sirküle eden sıcak su, kristalleştiricinin soğutma / eritme bölgesine sokuldu. Katı galyum tamamen eritildikten sonra, üç yollu anahtar ters çevrildi ve devridaim yapan soğutma suyu, soğutma / eritme bölgesine yeniden verildi; Sıcak su, sabit sıcaklıkta bir su tankı ve yerleşik bir sirkülasyon pompası kullanılarak sağlandı. Sıcaklık aralığı 278–373 K ve sıcaklık kontrolünün doğruluğu ± 1 K idi. Adımlar (Şekil 1c'de gösterildiği gibi), belirli bir kristalizasyon sayısına kadar tekrarlandı. Temizliğin tamamlanmasının ardından ürün kalitesi belirlendi.
Üç yollu bir anahtar değiştirildi ve dolaşımdaki sıcak su, kristalleştiricinin soğutma / erime bölgesine verildi. Katı galyum tamamen eritildikten sonra, üç yollu anahtar değiştirildi ve dolaşımdaki soğutma suyu tekrar soğutma / erime bölgesine verildi; Sıcak su, sabit sıcaklıkta bir su tankı ve dahili bir sirkülasyon pompası kullanılarak sağlandı. Sıcaklık aralığı 278-373 K ve sıcaklık kontrolünün doğruluğu ± 1 K idi.
Adımlar (Şekil 1c'de gösterildiği gibi) önceden belirlenmiş sayıda kristalizasyona kadar tekrar edildi. Temizliğin tamamlanmasından sonra ürün kalitesi belirlenmiştir.
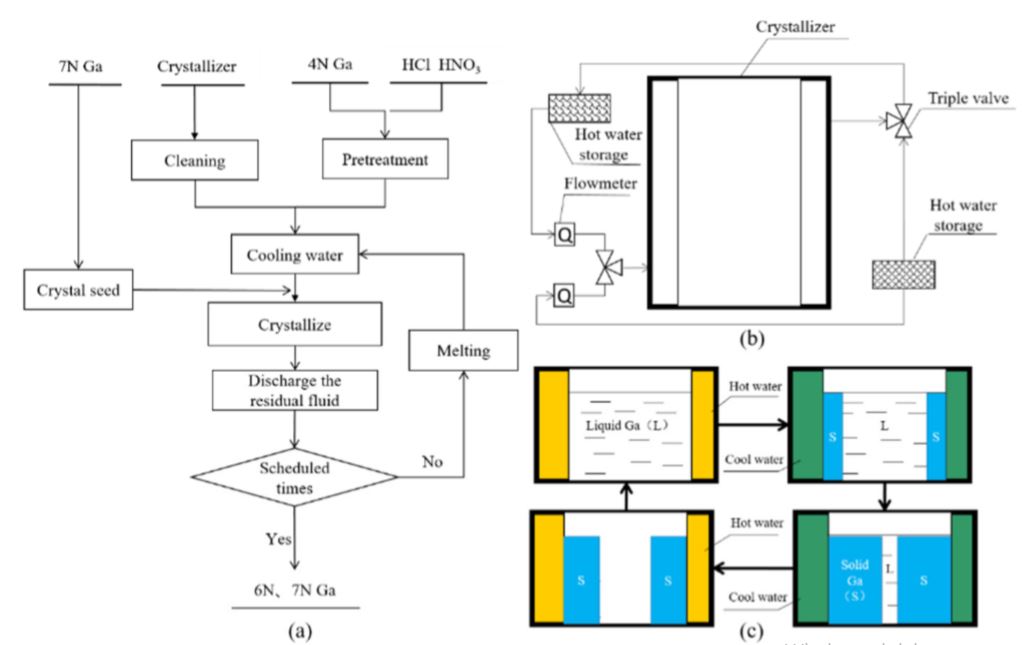
Şekil 1. Temizleme işleminin şematik gösterimi: (a) temizleme için işlem sırası, (b) temizleme cihazının montajı ve (c) tekrarlanan kristalizasyon işlemi.
2.2. saptama yöntemleri
Deneyde, 4N gallium hammaddesinin ve saflaştırılmış 6N, 7N galyumun safsızlık içerikleri, yüksek çözünürlüklü parıltı deşarj kütle spektrometresi (Evans Malzeme Teknolojisi (Shanghai) Co., Çin, HR-GDMS)) ile tespit edildi ve ürünün saflığı, fark metodu ile belirlendi. hesapladık. Algılama gazı olarak Argon kullanıldı. Kütle spektrometresi parametreleri aşağıdaki gibidir: boşaltma akımı 1,9 mA; Boşaltma voltajı 1 kV; Galyum iyonunun ışın akımı 1 × 10-6 mA; Yalıtım katmanı, alüminyum; ve çözünürlük ≥ 3600. Veri toplamadan önce, HR-GDMS iyon kaynağı, arka plan gazında iyon girişimini azaltmak için sıvı azot (90 K) sıcaklığına soğutuldu. Daha sonra, test edilen numunenin (0,2 x 2 mm 2) yüzeyi, 5 dakika boyunca sıvı yüzeydeki kirleticileri çıkarmak için bir sıvı azot sıcaklığında döküldü. Püskürmeden önceki koşullar sabit tutuldu ve veri toplama başlatıldı. Veri toplama sürecinde entegrasyon süresi 80 ms olarak ayarlandı.
3. Sonuçlar ve tartışma
3.1. Soğutma sıcaklığının tohum morfolojisi üzerindeki etkisi
265-295 K aralığında bir soğutma sıcaklığında üretilen tohum kristalinin görünüm morfolojisi, Şekil 2'te gösterilmiştir. Bu, 265 K'deki katılaşmış yapının birçok ince kristal tanesini içerdiğini ve tanelerin büyük miktarda sıvı galyum ile serpiştirildiğini göstermektedir. Katılaştırılmış yapı uzaklaştırıldığında, yüzeye çok miktarda sıvı galyum bağlanmıştır, 265 K'de çekirdeklenme sonrası kristal çekirdeğinin büyüme hızı bir kristal çekirdeği oluşumu ile sonuçlanan yüksek çekirdekli soğutma nedeniyle kristal çekirdeğinin büyüme hızı artmıştır. Çok sayıda dendrit bulunur. Dendritlerin hızlı büyümesi, yalnızca katılaşmış yapı içerisinde çok sıvı faz ile karışmakla kalmaz, katılaşmış yapının çok oyuk yüzeyine de neden olur. 273 K'nın bir hazırlama sıcaklığında, katılaşmış yapı, geometrik çokyüzlü şekil özelliklerini gösterdi; bu, süper soğutma derecesinin azalmasıyla kristal çekirdeğinin büyüme hızının düştüğünü ve büyüme modunun dendrit büyümesinden lameller büyümesine geçtiğini gösterir. Hazırlık sıcaklığı 278 K olduğu zaman, katılaşmış yapısı sıcaklığı, kristal çekirdekleri oluşumu sonrası büyüme ön süper-soğuma derecesi artan düşmeye devam önerir normal altı yüzlü bir şekle sahip, tabakalar büyüme ile ilgili büyüme modu değiştirilebilir. 295 K'nın bir hazırlama sıcaklığında, katı-sıvı ara-yüzünün süper-soğuma derecesi, kristal çekirdeğin oluşumundan sonra daha da azaldı ve gizli ısının kristalleşmesini önledi. Bu zamanda, kristal çekirdeğin büyüme yönü, yanalmaya dönüştü ve kristalizasyonun gizli ısısını daha hızlı bir şekilde serbest bırakmak için geometrik şeklini bozdu. Dört sıcaklıkta üretilen tohumların morfolojik özelliklerinin karşılaştırılmasıyla, tohumların optimum üretim sıcaklığı nihayet 278K olarak belirlendi. 273 K'lik bir üretim sıcaklığında, katılaşmış yapı, geometrik çok yüzlü şekil özelliklerini sergilemiştir; bu, süper soğutma derecesi azaldıkça, kristal çekirdeğin büyüme hızının azaldığını ve büyüme modunun, dendrit büyümesinden katmanlı büyümeye değiştiğini gösterir. Hazırlık sıcaklığı 278 K olduğu zaman, katılaşmış yapı artan sıcaklık düşmeye devam kristal çekirdek oluşumu sonra öne normal altı yüzlü bir şekle sahip, büyüme ön süper-soğuma derecesi ve büyüme modu dikey katman büyüme değişti. 295 K'nın bir hazırlama sıcaklığında, katı-sıvı ara-yüzünün süper-soğuma derecesi, kristal çekirdeğin oluşumundan sonra daha da azaldı ve gizli ısının kristalleşmesini önledi. Bu zamanda, kristal çekirdeğin büyüme yönü, yanalmaya dönüştü ve kristalizasyonun gizli ısısını daha hızlı bir şekilde serbest bırakmak için geometrik şeklini bozdu.
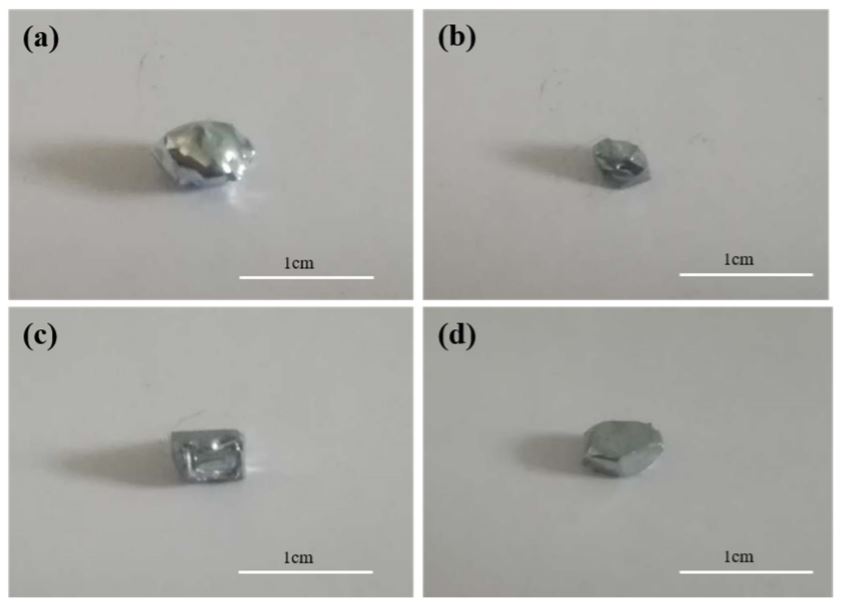
Şekil 2. Farklı soğutma sıcaklıklarında hazırlanan tohum kristallerinin morfolojisi ((a) 265 K, (b) 273 K, (c) 278 K ve (d) 295 K).
3.2. İşlem parametrelerinin kristalleşme sürecine etkisi
3.2.1. Soğutma suyunun sıcaklığının kristalleşme prosesine etkisi
Soğutma suyunun akış hızı 40 L · h-1 olduğunda ve sıcaklık, 288-298 K aralığında olduğu zaman, dekapajla ön işleme tabi tutulmuş ham galyum 2,9774 kg XIUMX, ardından 15 için tohum ilavesi kritik kritik noktaya soğutulur. dakika Karşılık gelen kristal büyüme morfolojisi, Şekil 3'te gösterilmiştir.
Şekil 3, soğutma suyunun sıcaklığı 288 ve 290 K olduğunda, sıvı galyum kristal büyüme modunun, tohum kristalinin eklenmesinden sonra esas olarak dendrit büyümesi olduğunu ve kristal dalların, kristalde sıvı galyumun sıkışıp kaldıklarında birbirleriyle köprülendiğini göstermektedir. Bunun nedeni, daha düşük bir soğutma suyu sıcaklığında, sıvı galyum içindeki sıcaklık gradyanının daha yüksek olması ve tohum kristalinin eklenmesinden sonra kristalin büyüme hızının daha hızlı olmasıydı. Bu sırada pozitif bir sıcaklık gradyanı oluşmasına rağmen, katı-sıvı ara yüzünün önündeki kristalleştiricinin radyal doğrultusundaki sıcaklık daha yüksekti, bu şekilde kristalleşme gizli ısısının serbest kalmasını önledi ve böylece bu yönde kristal büyümesini azalttı. Bununla birlikte, kristalizasyonun gizli ısısının serbest kalmasını kolaylaştırmak için, kristalin büyüme oryantasyonu değişti ve hızla dendritler şeklinde büyüdü, sonunda kristal dallarını kırarak ve köprü oluşturdu
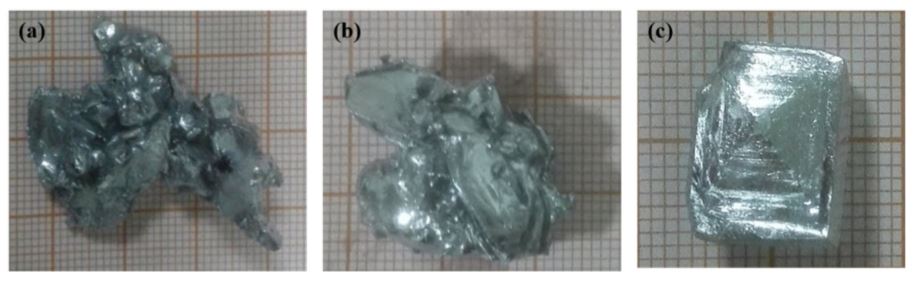
Şekil 3. Soğutma suyunun farklı sıcaklıklarında çekirdeklerin 15 dakika eklenmesinden sonra sıvı galyumun kristal morfolojisi ((a) 288 K, (b) 290 K ve (c) 293 K).
Sıvı fazın dahil edilmesi.
Tutulan sıvı faz kirletici maddeler kristal büyümesi nedeniyle uzaklaştırılamaz, bu nedenle arıtma işlemini etkiler. Soğutma suyunun sıcaklığı 293 K olduğunda, sıvı galyum tohum kristallerinin eklenmesinden sonra bir monokristara büyüdü.
Kristalizasyon sırasında sıvı galyumun büyüme yasasını daha fazla analiz etmek için, kristal çekirdeğinin eklenmesinden sonra, 40 L · h-1 K'nin soğutma suyu akışında dinamik zaman ölçümü yöntemiyle ve bir sıcaklık 293 K'de kristal morfolojisi çeşitli zamanlarda araştırılmıştır. Şekil 4'te gösterilmiştir.
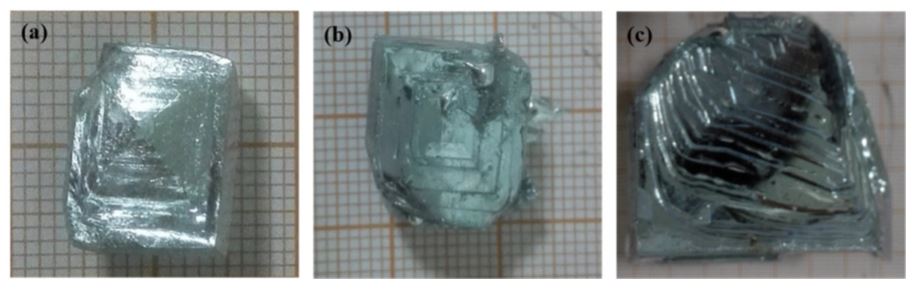
Şekil 4. Tohum eklendikten sonra farklı zamanlarda kristal blokların morfolojik görüntüleri ((a) 15 min, (b) 30 min ve (c) 60 min).
Şekil 4, tohumun eklenmesinden sonra galyum kristal külçesinin, artan kristalleşme süresi ile kademeli olarak arttığını ve tohum kristallerinin eklenmesinden sonra sıvı galyum kristal büyüme modunun, sıcaklığı gösteren tipik bir katmanlı kesme büyümesi sergilediğini gösterir, 293 K'de soğutma suyu tarafından oluşturulan bir gradyan ortamı olabilir. Kristal büyümesinin katı-sıvı ara-yüzünün ön tarafına gizli kristalleşme ısısı üretti ve bunları sıcaklık gradyanı dışına doğru aktarın ve serbest bırakın. Bu tip tabaka kristal büyümesi, katı madde elementlerinin katı-sıvı arayüzünden sıvı faza birikmesi için avantaj sağladı, böylece daha yüksek Ga katı Ga metal elde edildi. Büyüme zirvesinin süper soğuma derecesi, kristal büyüdüğünde ve katı-sıvı ara yüzündeki sıvı galyum atomları, tercihan, büyüme zirvesine bağlanmış ve ısı, kristalleştirici katı galyumdan, dışa doğru kristalleştirici içindeki pozitif sıcaklık gradyanına doğru aktarıldığı zaman, en büyüktü. , Bu nedenle, kristalizasyon işleminde kristal büyümesi her zaman kademeli bir ilerleme şeklinde bir piramidal formda olmuştur. Kristal büyümesinin kinetiğine ve termodinamiğine göre, katmanlı büyüme, kristalleşmenin gizli ısısının serbest kalmasını kolaylaştırarak ve kristalleşme işlemi sırasında kristallerin sürekli ve sabit bir şekilde büyümesini sağlayan, kristallerin yüzey alanını arttırmada elverişli olduğunu kanıtladı. Ek olarak, kristalde safsızlıkların ayrılma ve pıhtılaşma teorisine göre varsayılabilir.
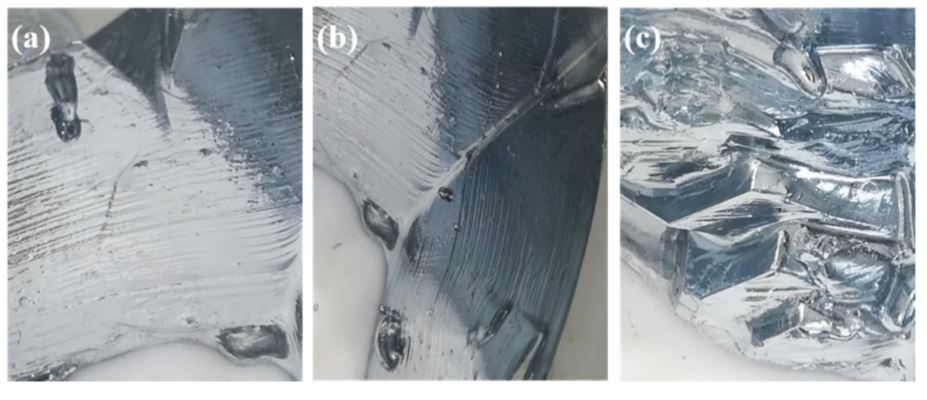
Şekil 5. (a) Kristalleştirici çıkışının yakınındaki 30 L · h · 1 için, (b) 40 L · h · kristalleştirici girişinin yanında 1 ve (c) kristalizatör girişinin yanında bulunan galyum kristalinin morfolojisi temiz geçit kristalizör.
Safsızlık elementlerinin katı-sıvı sınırdan sıvı halde zenginleştirilmesi ve düzensiz kristal büyüme yönü nedeniyle sıvı faz zarfları ile safsızlıkların önlenmesi. 4, kristalleşme zamanının artmasıyla kristalin piramit ucunun daha belirgin hale geldiğini ve kristal büyümesinin katmanlaşma adımının daha belirgin hale geldiğini ve kristalleşme devam ettikçe, safsızlık elementlerinin sıvı fazda sürekli biriktiğini ve saflığın katı-sıvı arayüzünde arttığını gösterir. katı-sıvı ara-yüzünün tutulabilirliğinin kristal büyüme zirvesini ne arttırdığı. Ga ile safsızlık elementleri arasındaki atomik yarıçap ve elektronegatiflik farkından ötürü, büyüme zirvesine bağlı safsızlık atomları Ga kafesini veya kafes boşluğunu istila etti ve Ga kristalinin büyüme kusuruna neden oldu. Bu, safsızlık elementlerinin uzaklaştırılmasının, kristalizasyonun ilerlemesiyle azaldığını ve literatür verileriyle çakıştığını göstermiştir.
3.2.2. Soğutma suyu akışının kristalleşme prosesine etkisi
Daha önce yapılan bir çalışmada, öncelikle soğutma suyu akışının kristalleşme süreci üzerindeki etkisi araştırılmıştır. Sonuçlar, kristalize edicinin çıkışı yakınında galyum kristalinin büyüme hızının, soğutma suyu akış hızı 30 L · h-1 olduğunda diğer bölgelere göre biraz daha düşük olduğunu gösterdi. Soğutma suyu akış hızı 50 · H - 1 olduğunda, kristalleştiricinin alt kısmındaki galyum kristalinin büyüme oranı, üst bölümünkinden biraz daha büyüktü ve kristalleştirici girişine yakın büyüme oranı en büyüktü. 40 L · h-1 soğutma suyu akış hızında, galyum kristallerinin büyüme hızı, kristalleştiricinin tüm bölgelerinde büyük ölçüde aynıydı ve hiçbir lokal büyüme olgusu çok hızlı ya da çok yavaş gözlenmedi. Bu işlem parametresinin kristalleşme süreci üzerindeki etkisini daha fazla araştırmak için, farklı soğutma suyu akışlarında sıvı galyumun kristal morfolojisi gözlemlenmiştir. Sonuçlar Şekil 5'te gösterilmiştir.
Bu, kristalleşme ilerledikçe, kirletici maddelerin sıvı fazda sürekli birikmesi ve katı-sıvı ara yüzündeki kirlilik içeriğinin artması, kristal büyümesi zirvesine bağlanan kirletici elementlerin olasılığını arttırması gerçeğine bağlanmaktadır. Ga ile safsızlık elementleri arasındaki atomik yarıçap ve elektronegatiflik farkından ötürü, büyüme zirvesine bağlı safsızlık atomları Ga kafesini veya kafes boşluğunu istila etti ve Ga kristalinin büyüme kusuruna neden oldu. Bu, artan kristalleşme ile safsızlık elementlerinin uzaklaştırılmasının azaldığını ve literatür verileriyle eşleştiğini göstermektedir.
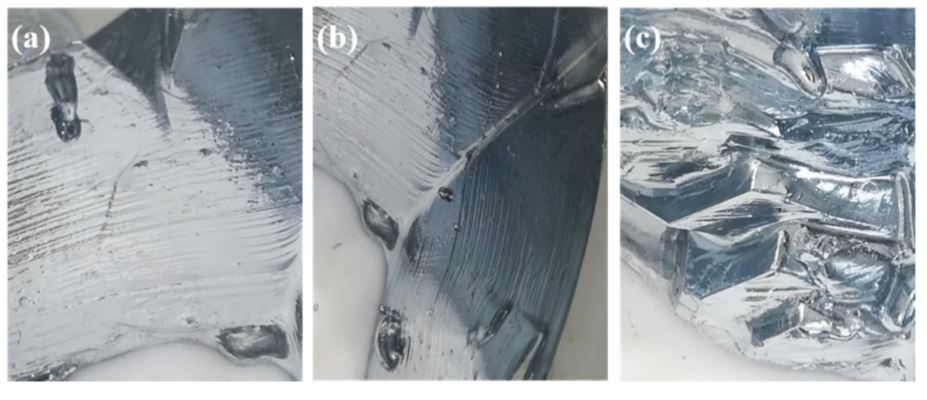
Şekil 5. (a) Kristalleştirici çıkışının yakınındaki 30 L · h · 1 için, (b) 40 L · h · kristalleştirici girişinin yanında 1 ve (c) kristalizatör girişinin yanında bulunan galyum kristalinin morfolojisi temiz geçit kristalizör.
Şekil 5, 40 L · h - 1 soğutma suyu çıkışına sahip galyumun kristal morfolojisinin, düzgün bir tane aralığı ile açık bir "kabuk deseni" gösterdiğini göstermektedir. Bu, galyum kristalinin bu akış hızında katman katman büyüdüğünü ve kirlenmenin giderilmesinde faydalı olduğunu gösterdi. 30 L · h - 1 soğutma suyu akışıyla, kristalleştiricinin çıkış tarafındaki kristal büyüme hızı diğer alanlara göre biraz daha yavaştı ve kristal morfolojisi 40 L · h - 1 soğutma suyu akışıyla aynıydı, ayrıca farklı bir "kabuk deseni" de görüntüleniyordu . Bu, bu akış koşulları altında galyum kristallerinin de katmanlar halinde büyüdüğünü gösterdi; bu, kirliliklerin giderilmesi için yararlıydı; Kristal büyüme hızı burada çevredeki alandan daha yavaştı, bu nedenle kristalleşme ilerledikçe sıvı fazı sarma olasılığı bu noktada göz ardı edilemez. Bununla birlikte, bir soğutma suyu çıkışı ile
Kristal büyümesi daha büyüktü ve kristal büyümesi daha hızlıydı, bu da kristal morfolojisini ve çok sayıda düzensiz büyüme adımının varlığını değiştirdi. Bundan, konumdaki kristallerin tamamen katmanlar halinde yetiştirilmediği ve kristal büyüme işlemine, dendrit veya peritektik oluşum eşlik eder ve bu da safsızlıklar ve katı galyum temizleme etkisini azaltan bir sıvı kabuk fazı ile sonuçlanabilir.
3.2.3. Mikrop sayısının kristalleşme sürecine etkisi
Soğutma suyu akışı 40 lh-1 ve bir 293 K sıcaklığıyla, kritik kristalleşme noktasına soğutulmuş sıvı galyum ilave edildi ve 3, 4, 5 ve 6 tohum kristalleri eklendi. Kristalleşme belirli bir seviyeye ulaştığında, morfolojik görüntüsü 6'te gösterilir; bu, eklenen tohum sayısının kristalleşmemiş alanın şeklini belirlediğini gösterir. Üç tohum kristali eklendiğinde, kristalleşmemiş alan üçgen şeklindedir. Dört çekirdek eklendiğinde, kristalleşmemiş bölge eşkenar bir şekil gösterdi. Bununla birlikte, eklenen kristal çekirdeğinin sayısı 3 veya 4 olduğunda, kristalleşmemiş bölgenin şekli ve boyutu uyuşmaz ve büyük bir tepesi ve küçük bir tabanı olan bir huni şekli gösterdi. Bu, kristalleştiricinin altındaki kristal büyümesinin sürekli kristalleşme ilerlemesi ile kesiştiği bir noktaya yol açtı; bu, sıvı fazın gelişmesine ve safsızlıkların dahil edilmesine neden oldu ve böylece deflatasyonun etkisini etkiledi. Beş tohum kristali eklendiğinde, kristalleşmemiş alan beşgen bir şekil gösterdi ve kristalleşmemiş alanda büyük bir üst ve küçük bir alt kısım ile şekil sorunu düzeldi. Altı tohum kristalinin eklenmesi durumunda, kristalize olmayan alan, düzenli şekil ve tek biçimli boyutta altıgen bir şekil göstermiştir ve ham galyumun saflaştırılması sırasında toplam kristal yönünün kontrol edilmesi için en avantajlı olmuştur. Bu nedenle, 4 N çiğ galyum saflaştırıldığında, kendiliğinden bir kristalleştirici kullanılarak optimum tohum ilavesinin altı olduğu tespit edildi.
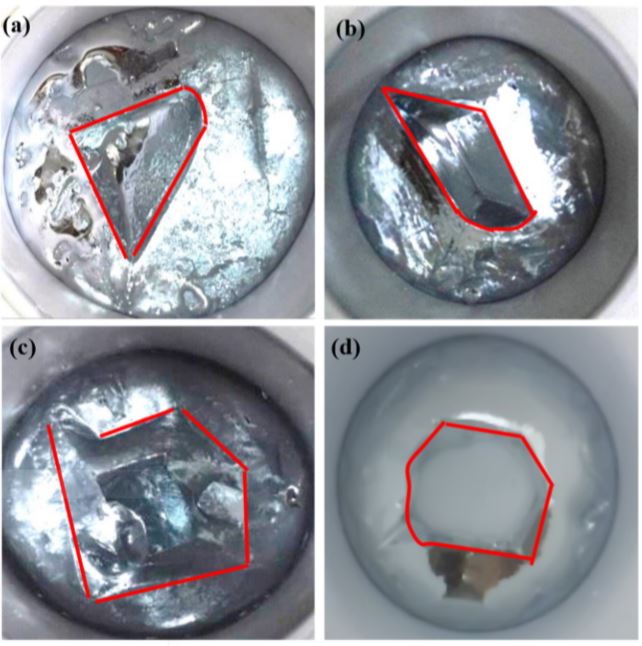
Şekil 6. Farklı sayıda çekirdek ((a) 3, (b) 4, (c) 5 ve (d) 6) ekleyerek kristal morfolojisinin fotoğrafları.
3.3. Proses parametrelerinin etkisi
3.3. Proses parametrelerinin kristalleşme hızına etkisi
Sıvı galyumun gerçek kristalizasyon katılaştırma işleminde, kristalleşme hızı (yani, çekirdeklerin eklenmesi üzerine galyumun kristal büyüme hızı) katı-sıvı ara yüzünün aşırı soğuma derecesine bağlı olmuştur. Katı-sıvı arayüzünün aşırı soğuma derecesi, diğer işlem koşullarını sabit tutmak için sıcaklık ve soğutma suyu akışının bir fonksiyonuydu. Deneyde, kristalleşme hızı ile soğutma suyu sıcaklığı ve akış arasındaki ilişkiler kontrol değişkeni yöntemi ile ölçüldü ve kristalleşme hızının deneysel kontrol formülü deneysel veriler analiz edilerek elde edildi. Deneysel hatayı azaltmak, deneysel kontrol formülünün doğruluğunu ve fiili üretim sürecine uyarlanabilirliğini artırmak için her ölçüm deney grubu dört kez tekrarlandı ve ortalama oluşturuldu. Deneyde ölçülen kristalleşme hızı, tohumun eklenmesinden sonra sıvı galyumun bütün katılaşma işlemi sırasında değiştirildi ve hesaplama formülü aşağıdaki gibidir:
v = m / t
v, ortalama oran, kg / sa; m toplam sıvı galyum kütlesidir, kg; t Sıvı galyumun tam katılaşması için gereken zaman, saat (s). Soğutma suyunun sıcaklığının ve akış hızının test tarafından belirlenen kristalleşme hızına etkisi 7'te gösterilmektedir. 7a, soğutma suyu sıcaklığı arttıkça, kristallenme oranının yavaş yavaş azaldığını ve aralarında açık bir doğrusal ilişkinin gözlendiğini göstermektedir. Kristalleşme hızı için soğutma suyu sıcaklığının deneysel kontrol formülü, Origin yazılımı özelleştirmesi ile elde edildi.
v (T) = -0,09 T + 27
burada T, soğutma suyunun K sıcaklığıdır; ve veri uyumunun doğrusal korelasyon katsayısı, R2 = 0,997 idi. 7b, soğutma suyunun akış hızı arttıkça, kristalleşme oranının arttığını ve ikisi arasında önemli bir üstel fonksiyonel ilişkinin gözlendiğini göstermektedir. Origin yazılımı ile soğutma suyu akışının kristalleşme hızına yönelik deneysel kontrol formülü elde edildi.
v (Q) = -96,73e - Q 4,94 + 0,66
Q, soğutma suyunun akış hızıdır, L / s; ve veri uyumunun standart sapması R2 = 0,997 idi.
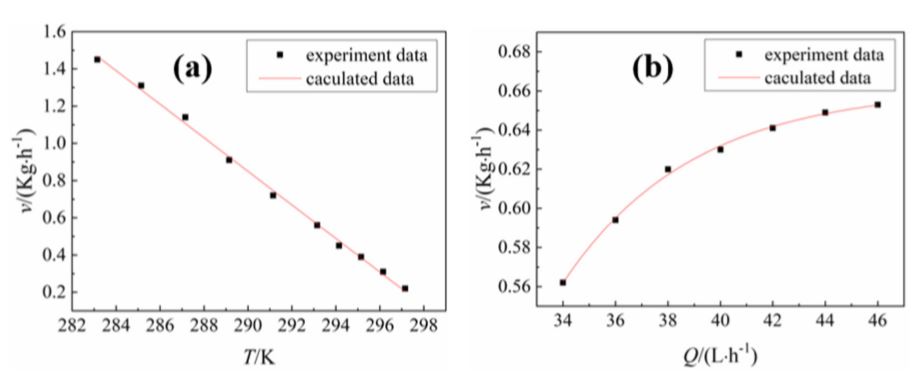
Şekil 7. (a) Soğutma suyu sıcaklığının, 40 L · h-1 akış hızında kristalleşme hızı üzerindeki etkisi; (b) 293 K'deki Soğutma Suyu Akış Hızının Kristalleşme Hızı Üzerine Etkisi
3.4. Temizleme sonuçlarının analizi
Yukarıdaki araştırmalara dayanarak, 4N ham madde galyumunun kristal saflaştırılması için optimal teknolojik parametreler şu şekilde belirlendi: Tohum preparasyonunun sıcaklığı, 278 K; Soğutma suyu sıcaklığı, 293 K, soğutma suyu akış hızı, 40 L · h-1 ve eklenen tohum kristallerinin sayısı altı oldu. Önceki araştırmamızla birlikte, üç temizleme planı oluşturuldu
Üç saflaştırma şeması tarafından hazırlanan yüksek saflıktaki galyumdaki safsızlık seviyeleri test edildi ve galyum ham maddesi ile karşılaştırıldı ve safsızlıkların uzaklaştırılma oranı hesaplandı. Sonuçlar Tablo 2'te gösterilmiştir.
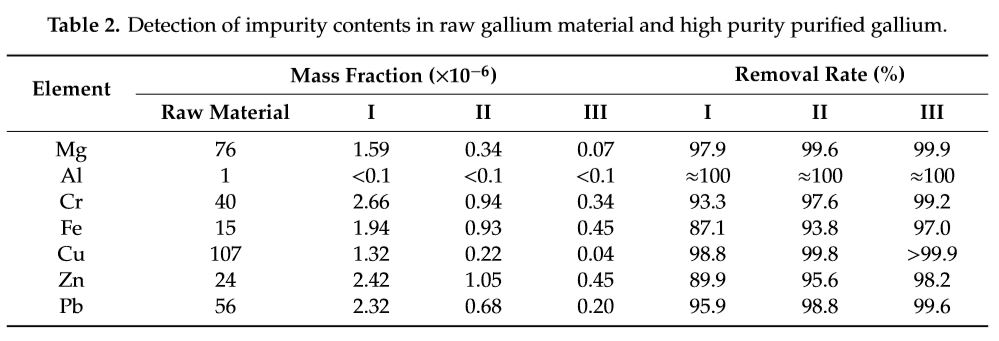
Tablo 2. Galyum hammaddesi ve yüksek saflıkta saf galyum içerisindeki kirletici madde seviyelerinin tespiti.
Tablo 2, saflaştırmadan sonra, malzemelerde bulunan safsızlık fraksiyonlarının HR-GDMS tespit sınırının altına düştüğünü ve diğer altı ana safsızlığın da iyi bir şekilde çıkarıldığını göstermektedir. Kaldırma oranları:% Fe-87,1,% Pb-95,9,% Zn-89,9,% Mg-97,9,% Cu-98,8, ve% Cr-93,3, ve fark yöntemiyle hesaplanan alüminyum metalinin kütle oranı% 99,999987 idi.
Şema II için altı ana safsızlığın ayrılma oranları% Fe-93,8,% Pb-98,8,% Zn-95,6,% Mg-99,6,% Cu-99,8 ve% Cr-97,6% ve ana Ga metalinin kütle fraksiyonu% 99,9999958 idi , Şema III için, altı ana safsızlıktan arınma oranları artmaya devam etmiş ve Mg ve Cu uzaklaştırma oranları% 99,9'i aşmıştır. Buna karşılık, Fe çıkarma oranı, en düşük seviyede iken, aynı zamanda% 97'e ulaştı. Ana metal Ga'nın kütle oranı% 99,9999958 idi.
4. sonuçlar
Özetle, incelenen Ga'nın safsızlığının ayrıntılı olarak ortadan kaldırılması ve bu kristal indüksiyonunu kullanarak kristalizasyon saflaştırma işleminin gerçekleştirilmesi önerilmektedir. Soğutma sıcaklığının, kristalin morfolojisi ve soğutma suyu sıcaklığı, akış hızı ve incelenen kristalizasyon işlemine eklenen çekirdek sayısı üzerindeki etkisi. Optimum temizleme yöntemi elde edildi; kristalleşme oranının kontrol denklemi belirlendi; ve yüksek saflıkta (6N ve 7N) galyum teknolojik koşullar altında üretildi. Bu çalışmanın ana sonuçları aşağıdaki gibidir:
- 4N hammadde galyumunun kristalizasyon saflaştırması için optimum işlem parametreleri aşağıdaki gibidir: tohum hazırlama 278 K'nin sıcaklığı; Soğutma suyu sıcaklığı 293 K; Soğutma suyu akışı 40 L · h - 1; tohum kristallerinin sayısı altı 6 ekledi;
- Kristalleşme hızı artan soğutma suyu sıcaklığıyla doğrusal olarak azaldı ve artan soğutma suyu akışı ile üssel olarak arttı. Soğutma suyu sıcaklığı (T) ve kristalleşme hızı v üzerindeki Q akış hızı kontrol formülleri şunlardır: v (T) = -0,09T + 27 ve v (Q) = -96,73e -Q 4,94 + 0,66;
- Önerilen üç temizlik programı, kirletici elementleri etkili bir şekilde kaldırdı. 4 ham nikelini saflaştırmak için Şema I kullanılırken, bir 6 N saflığına sahip yüksek saflıkta galyum elde edildi. Şema II ve III kullanılarak, 7N yüksek saflıktaki galyum içerisine verildi. Şemalar I, II ve III tarafından hazırlanan yüksek saflıkta galyum saflıkları sırasıyla% 99,999987,% 99,9999958 ve% 99,9999958 idi.
Çalışmada önerilen tohum kaynaklı radyal kristalizasyon yöntemi, işlem kolaylığının, uygun işlem akışının, düşük enerji tüketiminin, çevre dostu ve kolay uygulama işleminin otomatik kontrolünün avantajlarını sunar ve yüksek saflıkta galyumun büyük ölçekli endüstriyel üretimi için yeni bir fikir sunar. ,
Nadir toprak metalleri Enstitüsü
Kimya ve Kimya Mühendisliği Bölümü, Lvliang Üniversitesi, Çin
Metalurji Okulu, Kuzeydoğu Üniversitesi, Shenyang, Çin